Netherlands researchers have come up with a concrete solution to address the shortage of housing in the nation – by printing new dwellings.
Eindhoven University of Technology, a technical and research university in the countryโs south that specialises in engineering science and technology, is leading the way with Project Milestone.
According to the university, printing can drastically reduce raw material consumption and is forecast to greatly increase the speed of construction in the future.
Projectย Milestoneโs website has said it is the โworld’s first commercial housing project based on 3D-concrete printing”.
On the weekend, the project celebrated its own milestone, with the first residents – Elize Lutz and Harrie Dekkers – inspecting a 3D-printed property in Eindhovenโs Meerhoven district.
The house โ the first of five in Project Milestone โ is shaped like a boulder to blend in with its surroundings and is reminiscent of a home from The Flintstones’, but with a sleek, modern interior.ย
It also fully complies with the Netherlandsโ strict building requirements.
Eindhoven’s Technical University Professor, Theo Salet, had to overcome myriad disappointments throughout the research process, including the trial and error of finding the right combination of concrete and insulation material for the sandwich walls.ย
But equally, he was rewarded when he has realised his team was making progress.
ITโS A MATTER OF NECESSITY
Prof Salet has led the joint construction and innovation project for years.
He has worked alongside PhD students Rob Wolfs and Zeeshan Ahmen, as well as various masterโs students and third parties, and was quick to point out that โthis is not about the ambition of some scientistโ.
โItโs about the rock-hard necessity of making major changes to the way we build,โ Prof Salet said.
โWe need to build in the Netherlands alone a million homes in 10 years and make 7.5 million homes drastically more sustainable in 30 years.
โIn addition, infrastructure from the 1960s and 1970s is heading towards the end of its design life. We are facing an unprecedented challenge.โ
The five houses of Project Milestone are being built in succession so each new round of construction can maximise the learning opportunities from the previous.ย
Soon, the project partners will begin work on the design of the next homes, which will have multiple floors and therefore require further development of the technique.
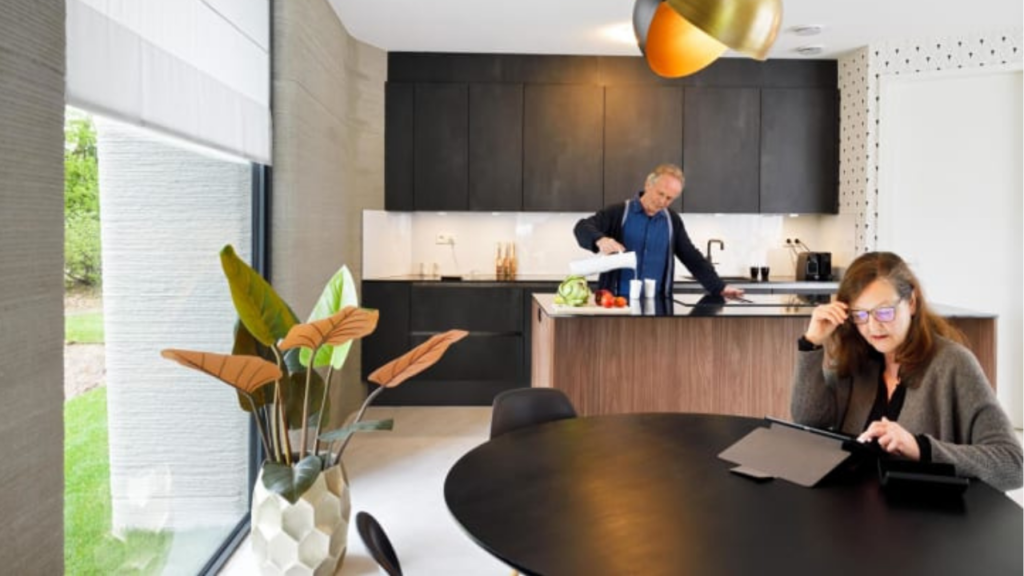
HOW IT WAS BUILT
The house comprises 24 printed concrete elements that have been printed layer by layer at the printing plant in Eindhoven.
The elements were transported by truck to the building site and placed on a foundation. The house was then provided with a roof and frames, and the finishing touches applied.
The project took a year to complete but the printing process itself took about 120 hours.
โThe fact that weโve already come this far makes me a proud man,โ Prof Salet said when he inspected the property last weekend.
Prof Salet also said he was proud of how the knowledge developed has found its way to industry so quickly.
He said producing a complete house was a vastly more complicated process than printing a wall and could only be done with the right industrial partners.
โWhatโs nice is that thereโs still so much to be gained just by learning from this experience,โ he explained.ย
As for the prospective tenants, Mr Dekker conceded it was an “unusual” dwelling but said he and Ms Lutz were looking forward to moving in later this year.
“We are always looking for special places to live,” he told CNN.
It was a sentiment echoed by Ms Lutz.
“It reminded me of a special way of living,” she said. “It looked very safe.”